Reference customer Farm am Eulenbruch | Wood chips to high-quality energy pellets
- Marketing Ecokraft
- Oct 24, 2023
- 5 min read
Updated: Oct 30, 2023
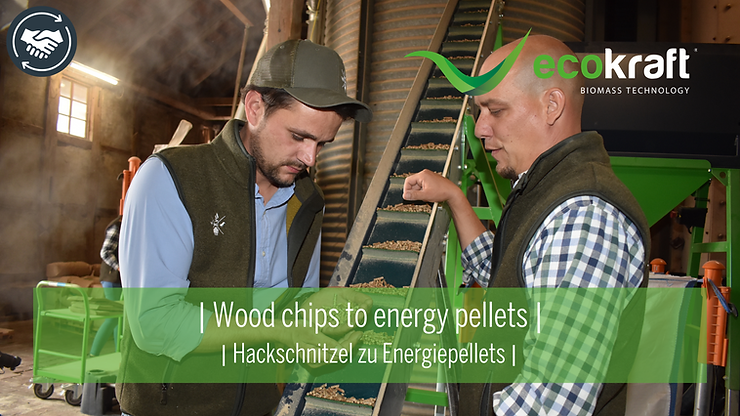
In the last three years, the focus at the Eulenbruch Farm (www.boese-farm.de) in Hespe, Lower Saxony, has shifted towards the energy sector. "Autarky has become the most important thing to me. It provides me with peace and planning security," says Hannes-Friedrich Böse. The state-certified agricultural business manager wanted to be independent of the world market when it comes to energy. "I saw my future in specializing in renewable resources from the region and providing them to people in the region. I've succeeded in establishing this planning and working foundation," says the 32-year-old, who is well aware that energy is becoming scarcer and more expensive. The farm's main focus in this area is on the production and marketing of wood chips and, since August 2022, wood pellets, manufactured with the pelletizing system from the company Ecokraft.
Hannes-Friedrich Böse took over the family farm in 2020, which has a remarkable history dating back to 1620. The conventional mixed-use farm is involved in crop farming and poultry farming. With the takeover, the young man also intensified his focus on wood chips and wood pellets as high-quality fuels and environmentally friendly alternatives to conventional energy sources.
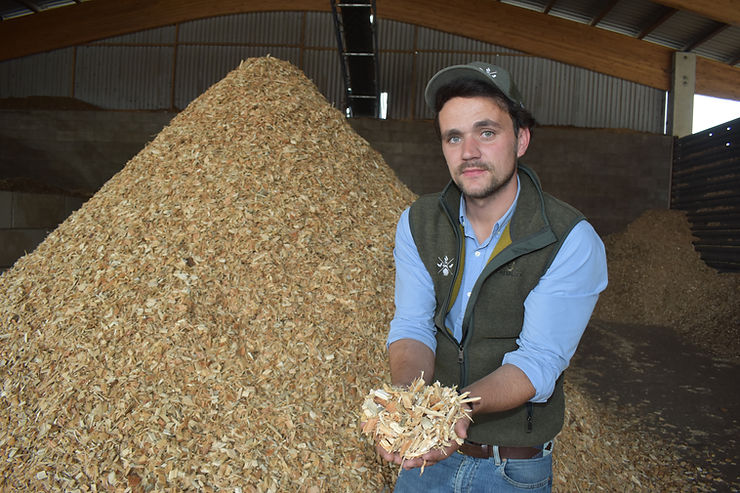
Figure 1: Hannes-Friedrich Böse with his wood chips
For nine years, the farm has had a wood chip heating system with an in-house heating network. The foundation for this system is primarily wood chips from municipalities, as well as private, state, county, and federal forests within a 20 km radius, in addition to the farm's own wood resources. The acquisition is done in collaboration with JB Erdbau, led by his brother Jan-Christoph. Both share the task of acquiring customers, after which the earthworks company produces and delivers the product. In addition to utilizing residual wood, partially non-timber-worthy timber also serves as a basis.
The farm's wet storage area can hold around 2000 m3 of wood chips. Currently, the farm processes 30,000 m3 of quality G 30 to G 50 wood chips each year. The wet product stays in storage for a maximum of one week before going into the drying process. A telescopic loader lifts the wood chips into a storage bunker leading to the Riela push-turn dryer. The continuous dryer is 14 meters long and 2 meters wide, with a drying capacity of 400 kW, reducing the moisture content of the wood chips from 55% to 15-20%. In the push-turn dryer, 70°C hot air is blown through the material, constantly turning the wood chips with rakes. The moist air is extracted, the dust is filtered, and clean air is released outside. "The drying process is fully automated and has been running autonomously for two and a half years, 365 days a year. We only refill the bunker in the morning and evening," says the farm manager.
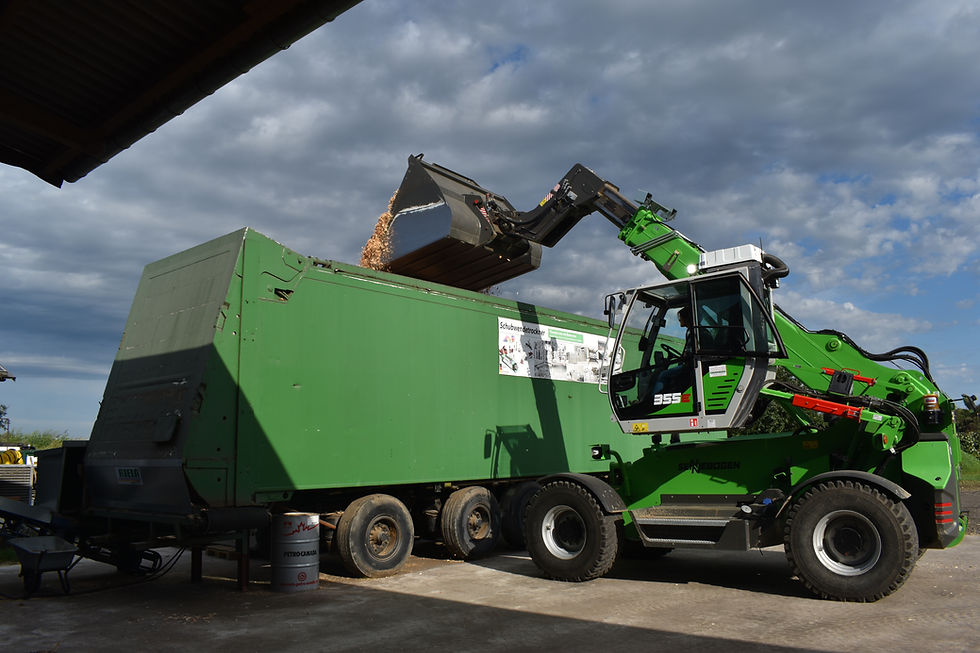
Figure 2: Filling the push-turn dryer
Every day, 150 m3 of wood chips are dried. On average, 100 m3 are required per day, with 50 to 60 m3 for their own use, and the rest is sold. The ready-to-use wood chips are stored in the hall until they are marketed or processed for private and industrial customers and heating power plants.
Starting in early October, the drying facility is used to dry corn for two to two and a half months - a total of 3500 tons, with 700 tons being their own corn and the rest split evenly between drying services and purchased materials from a QMS-certified agricultural products trading company. The corn is dried from 30% to 15% moisture content and is then marketed to feed mills within an 80 km radius, where it can be stored and processed.
To ensure a buffer during this time, sufficient wood chips are dried and stored in advance. Afterward, the dryer is cleaned, and the tools inside the dryer are replaced with paddles.
Previously, wood chip plants were supplied with wood chips. "Then I got the idea to take this path into my own hands and build another pillar for my business," Hannes-Friedrich Böse explains. In his search for a solution, he found Ecokraft online, researched extensively, and eventually entered into business with the specialized company. Initially, the farmer thought about getting a single system but ultimately decided on a dual system with a production capacity of 500 to 600 kg per hour. "I took a certain risk, but I saw a corresponding market for it, and in retrospect, it was a good decision," reveals the entrepreneur. The key factor for choosing Ecokraft was the flexibility to pelletize various materials with this system. "Who knows how the market will evolve. With the right die, I can react flexibly and pelletize hay, straw, or sheep's wool," the 32-year-old explains.
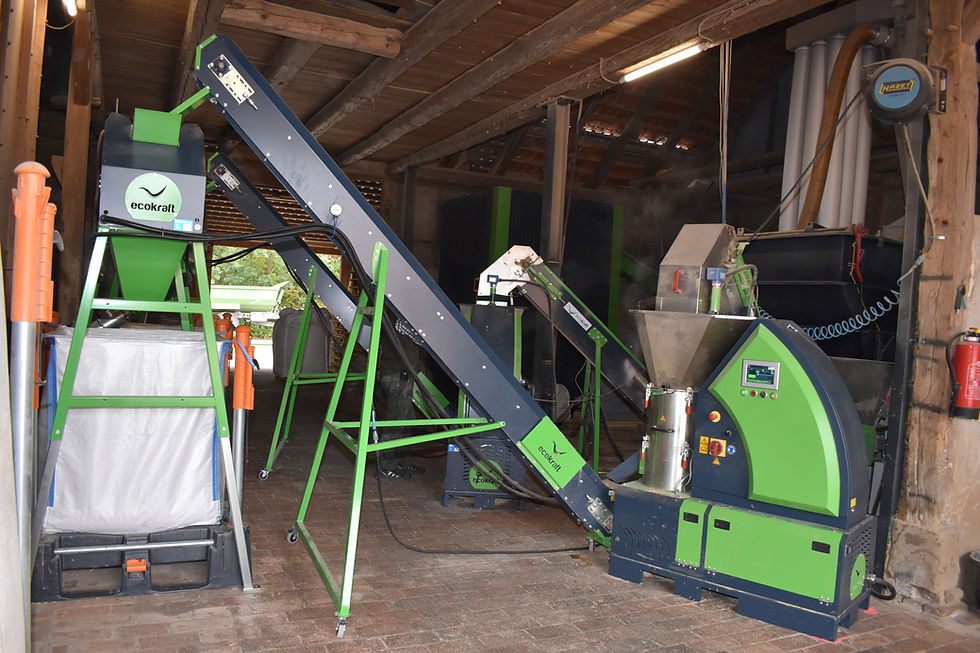
Figure 3: Ecokraft DUO-Pelleting line
Due to the market situation in recent years, a customer base was quickly established, and the wood pellet business continues to thrive. The advantages of pellets are their transportability, storage capacity, space-saving nature, and low labor requirements, making them attractive to private consumers.
The initial phase with the pelletizing system was somewhat turbulent, but with the manufacturer's help, the right dies were quickly found, and the raw material was optimized to get the most out of the machine. "I appreciate the excellent service as well as the competent and personable contact persons who treat me as an equal," emphasizes Böse.
The pelletizing system is housed in a grain barn with a storage capacity of 600 tons. The processes and workflow have become more efficient over time, requiring few replacement parts. Around 15% of the wood chips are processed into pellets, which equates to 5 to 6 tons per day. The system currently runs 220 days a year, with 5 m3 of wood chips producing one ton of pellets.
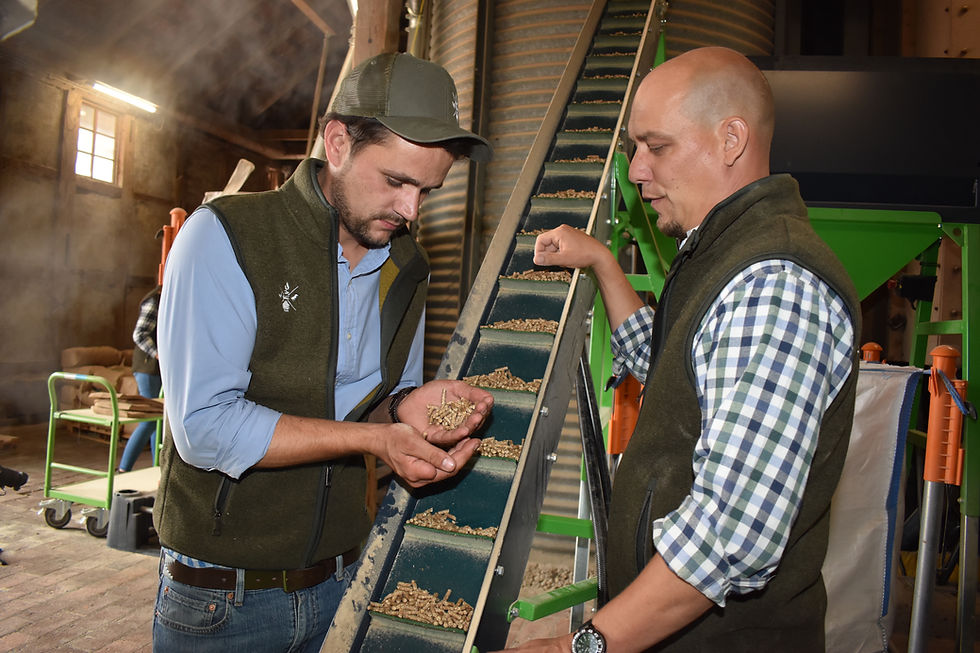
Figure 4: Hannes-Friedrich Böse with fresh energy pellets from the Ecokraft DUO pelleting plant
The wood chips are fed into the Ecokraft system from a storage bunker via a conveyor belt and are then cut to 4 mm in the cutting mill. The material then goes into another storage bunker. Before pressing, corn starch is added to make the pellets shiny and hard, reducing energy consumption. In the press, the raw material is processed into pellets under high pressure and temperature. These pellets are further transported using a conveyor belt and are sent to high silos after small particles are sieved out.
The pellets are finally packed in 15 kg paper bags, and customers take them with a deposit system – exclusively private customers from the area where the raw materials are sourced, who purchase between ten bags and 15 tons. "This way, we achieve regional sustainability in the energy sector," adds the farmer. His deposit system idea emerged while filling a bunker and has been well-received by customers. They return the bags, which can be used up to three times, and receive credit for their next order. "I don't make money from this, but I value the idea of sustainability," explains the businessman, who values a fair approach with his customers under the motto "live and let live."

Figure 5 : Hannes-Friedrich Böse with his energy pellet products
Together with four full-time employees, Hannes Friedrich Böse manages the tasks at hand. "The decision to enter pellet production was right and good. In combination with photovoltaic and the biomass CHP plant, we achieve energy independence and competitiveness for the future, providing planning security," says Böse. Through sustainable investments, he has achieved internal thermal and electrical independence. The wood CHP plant is a wood gasifier CHP that converts woody biomass into combustible gas. A generator further refines it into electrical energy. The waste heat is used in the farm's internal heating network to provide for the farm and residential buildings, as well as the wood drying system. With the CHP plant, energy generation is guaranteed regardless of weather and wind.

Figure 6: Hannes-Friedrich Böse with his at his Eulenbruch Farm
For the past two years, Hannes-Friedrich Böse and his girlfriend Luisa have opened the historic, 170-year-old bakehouse for civil and free weddings. This service is well-received, with around 30 weddings taking place each year. Catering is also provided for guests in the idyllic garden upon request.
His plans for the future include expanding marketing, acquiring new customers, and establishing a district heating network for residential and commercial buildings in the area.
Website Farm am Eulenbruch: www.boese-farm.de
- Helga Gebendorfer -