top of page

Wood & types of wood
Heating with wood pellets from sustainable forestry is inexpensive, energy-saving and climate-neutral.
-
Wood chipsInexpensive, energy-saving and climate-neutral heating with wood pellets from sustainable forestry. The trend towards pellet heating systems is unbroken. Be it the replacement of the outdated oil heating or the new installation. As a result, the demand for wood pellets is constantly increasing: in the last 10 years alone, sales of wood pellets have quadrupled. Until now, energy pellets were mostly made from 100% pure spruce heartwood (debarked). However, the demand for industrial pellets from by-products from wood and sawmills, i.e. screen material, sawdust, shavings, residual wood and also wood chips, is also growing steadily. To produce one ton of wood pellets, about 6 to 8 cubic meters of chips or about 4 cubic meters of wood chips are required. The raw material may have a maximum moisture content of approx. 20%. Container drying is ideal for drying wood residues. This simple and inexpensive process can dry a volume of approx. 27 cubic meters from approx. 60% to below 20% residual moisture in 8 to 12 hours. All wood materials under 6 mm can be pelletized immediately, all other sizes must first be cut up in a cutting mill. Then, under high pressure, the material is pressed through a die with rotating rollers (roller wheels). Due to the resulting heat, the material's own resins and lignins bind the pellet perfectly, so no additional binding agents (pressing aids such as vegetable starch) are necessary for softwood. Before cooling down in special mosquito net big bags, the pellets produced can be sieved to reduce the fines content. After a cooling break of 8 to 12 hours, the wood pellets are then fully hardened and can be packaged or transported in silos. The energy required to produce pellets from dry sawdust is only 2.7%. In comparison, the production of heating oil consumes 12% and liquid gas even 14% of the energy. The calorific and calorific value of these energy pellets is very good, only the ash content is usually slightly higher due to the bark content that is also processed. The wood residues used are greatly reduced in volume and dust due to the strong increase in bulk density. The risk of a dust explosion is significantly reduced. Wood pellets can be easily and cheaply transported, stored and precisely dosed in heating systems via augers and/or suction systems. 2 kg of wood pellets replace approx. 1 liter of heating oil. Wood pellets are a sustainable, regionally available and inexpensive source of energy that is good for the climate and makes us all a little more independent.
-
SawdustA waste product becomes high quality fuel! In the wood processing industry, large amounts of sawdust are produced every day.These are usually disposed of or sold very cheaply as bedding material for animal husbandry. A quick example: Sawdust is sold for approx. 11 to 15 euros/m³ (weight approx. 220 kg/m³), which results in a sales price of approx. 60 euros/to. Instead, a ton of wood pellets is sold for around 260 euros, so an additional profit of around 200 euros/to could be realized just by changing the density and shape. Machine amortization times of less than a year are not uncommon here! This also applies to wood chips or shavings. With our process, you can produce first-class wood pellets for your own use or for sale - without a large number of personnel, almost fully automatically. By simply swapping our matrices, you can choose the desired diameter of 6 mm (standard), 8 mm or even 20 mm. Areas of application for the pellets: - Energy production- Litter 2 kg of sawdust result in approx. 10 kw/h of energy, which in turn corresponds to approx. 1 liter of heating oil! During the pelleting by our Ecokraft pelleting machine model series, almost 80 degrees Celsius arise during processing, which brings the biomass into the desired shape and makes it durable for a long time. 3 parts of sawdust correspond to approx. 1 part of pellets, which means that the required storage space is reduced by approx. 67%! All pelleting machine models are characterized by their excellent workmanship (100% Made in Germany) and high production quality in continuous operation. In addition, on chem. Binding agents are completely dispensed with in the manufacture of the pellets.
-
Maple dustsMaple dust and flakes into wood pellets People love the maple structure and color, especially for doors and furniture, but valuable energy pellets can also be obtained from the dust and flakes from the production facilities. 2 tons of wood pellets usually replace 1,000 liters of heating oil as a 100% climate-neutral energy source.
-
Wood chips, dust and flakesMany timber construction companies invest in fully automated, computer-controlled cutting and joinery systems. Enormous quantities of chips, flakes and dust are produced during the treatment and further processing of building and construction timber. Up to now, these biogenic waste materials have often not been used or only used to a very limited extent. In many cases, they even paid for collection and disposal. But it is precisely this waste wood, usually softwood with a residual moisture content of 10-15%, that lends itself very well to pelleting. The material can be screened in a cutting mill and crushed to a maximum size of 6 mm. This is followed by pelleting into energy pellets with a calorific value of 4.5 kW/kg to 4.9 kW/kg. Key advantages for converting to energy pellets: - Avoidance of the so-called dust explosion, the dust is converted into solid pellets and the danger is averted - Saving of storage space through extreme volume reduction of approx. 8 : 1 - Saving of collection and disposal costs, since fewer trucks collect the material and bring it to landfill/incineration - Saving heating costs through self-sufficiency - Additional income opportunity through the sale of pellets - Increase of independence, the production and supply of fuel can be done on site - Increase in sustainability by using operational resources and avoiding waste (wood waste becomes valuable material again)
-
Pine dustPine dust and flakes into wood pellets Pine dust and flakes are ideal for use as energy pellets. 2 tons of wood pellets usually replace 1,000 liters of heating oil as a 100% climate-neutral energy source.
-
CelluloseCellulose is an important raw material for paper production (raw material is wood rich in lignin and cellulose) as well as for the chemical industry and the clothing industry (seed hair of the cotton bush and bast fibers from flax, etc.). In nature, cellulose is available in large quantities, which is why research is currently being carried out into whether and to what extent biofuel can also be produced from plant biomass (wood and straw). The excellent building physiology properties of cellulose also make it a coveted bulk and insulating material. Areas of application for the pellets: Fuel Bulk material Insulation material During the pelleting by our Ecokraft pelleting machine model series, almost 80 degrees Celsius arise during processing, which brings the biomass into the desired shape and makes it durable for a long time. All pelleting machine models are characterized by their excellent workmanship and the permanent high-performance output. In addition, we completely dispense with binding agents in the production of pellets and are thus clearly distinguishable from the market!
-
Root woodRoot to energy pellets In the first step, the root wood is cleaned and then processed into industrial pellets. The calorific value of root wood is only approx. 15% below that of premium spruce pellets.
-
OakOak (dust and shavings) to energy pellets Hardwood was generally considered difficult to pellet because of the low lignin content in the wood. In the manufacture of solid wood furniture, however, very large amounts of dust and chips are produced. To date, these biogenic residues have often not been used or only to a very limited extent. In many cases, they even paid for collection and disposal. Oak has a very high energy potential with a calorific value of up to 5.3 kW/kg. This means that 2kg of oak pellets could replace one liter of heating oil. Key advantages for converting to energy pellets: Avoidance of the so-called dust explosion, the dust is transformed into solid pellets and the danger is averted Saving of storage space through extreme volume reduction of approx. 4:1 Saving of transport and disposal costs for disposal by third parties Saving heating costs, through self-sufficiency Additional income opportunity by selling the pellets Increase of independence, the production and supply of fuel can be done on site Increase in sustainability by using operational resources and avoiding waste (wood waste becomes valuable material again)
-
Disposable palletsDisposable pallets for energy pellets One-way pallets are solid pallets made from A1 waste wood that are used for the transport from the manufacturer to the customer and for the storage of goods. They are essential in the transport and logistics industry because they are cheap, easy to maintain and sturdy. The only disadvantage: they can usually only be used once. If goods are delivered on disposable pallets, the pallet remains with the recipient and must be disposed of at the expense. One-way pallets are cheaper and lighter than Euro pallets and can also be produced in special sizes, which reduces the transport weight and the need for loading space. It is therefore usually more economical to use disposable pallets than to deliver and pick up the goods on expensive Euro/reusable pallets. However, in order to avoid the high disposal costs and the unnecessary waste of these one-way pallets, pelleting these pallets into heating pellets is a very good idea. In a hacker, the pallets are pre-shredded in the first step and then pass through a double magnetic separator and a stone trap to remove nails and stones. The material is then chopped up again in a cutting mill to a maximum size of 6mm. The last step is pelleting into energy pellets with a calorific value of 4.5 - 4.9 kW/kg, which are then profitable can be sold. This not only saves a lot of money, but also does something for the environment at the same time. Key benefits of converting to energy pellets:- Saving of storage space through extreme volume reduction - Saving of collection and disposal costs - Savings on heating costs through self-sufficiency - Additional income opportunity through the sale of pellets - Increase in independence, the production and supply of fuel can be done on site - Increasing sustainability by using operational resources and avoiding waste
-
Demolition woodWhen buildings and houses are demolished, considerable amounts of demolition wood are produced. This includes used wood such as treated old wood, window frames without panes, floors such as wooden parquet or floorboards, old kitchens as well as doors and delivery pallets made of wood materials. The disposal of this demolition wood is usually very expensive, since transport and disposal costs are doubled. Up until now, wood has hardly ever been used more than once in construction – when it is, it is shredded into chipboard. However, the Circular Economy Act stipulates that the recyclable material wood should be kept in the cycle for as long as possible and thus be used several times. Because there is still a lot of potential in waste wood: according to this, wood and wood products should be used longer than before in the economic cycle and recycled more efficiently. This saves resources and increases the climate protection effect of using wood. Around 8 million tons of waste wood accumulate in Germany every year. Around 20 percent of this is recycled and processed into chipboard. Most of the remaining waste wood is used for energy. It is either used in waste wood power plants to generate heat or, to a lesser extent, in wood processing companies themselves to generate energy. If pollutants are present - mostly due to paints, varnishes, coatings or because the wood contains wood preservatives - these are difficult to remove from the wood. Most of the time everything ends up in incineration. The incinerators are equipped with appropriate filters. In order to optimally reuse this wood and at the same time save storage space, transport and disposal costs, this valuable material can also be processed into marketable industrial energy pellets and thus returned to the economic cycle.
-
Wood pellet dustHeating pellets are usually stored in large wood pellet stores. When the wood pellets are delivered, the pellets are filled into the pellet store using the so-called blow-in process. This injection process creates fines in the pellet store. As a result of the demixing process during discharge, the fines end up in the lower area of the pellet store over the course of time. When cleaning the wood pellet store, both this fine fraction should be removed, as well as the wood dust that has settled on other surfaces. In order to ensure optimal functioning of the pellet heating system, the wood pellet store should be completely emptied and the fines removed every two years or after two or three deliveries at the latest. However, this fine material should not be disposed of, but can be converted back into new energy pellets in a resource-saving manner. Advantages of re-converting to energy pellets: - Increase in sustainability by using operational resources and avoiding waste (waste material becomes valuable material again) - Saving of storage space through extreme volume reduction - Saving of transport and disposal costs - Savings on heating costs through self-sufficiency - Additional income by selling the pellets
MATERIAL TEST
Do you have questions about pelleting or are you unsure which solution suits you?
Call us at +49 9962 86734-0,
email us at: office@ecokraft.com
or fill out our inquiry form.
We are happy to help!
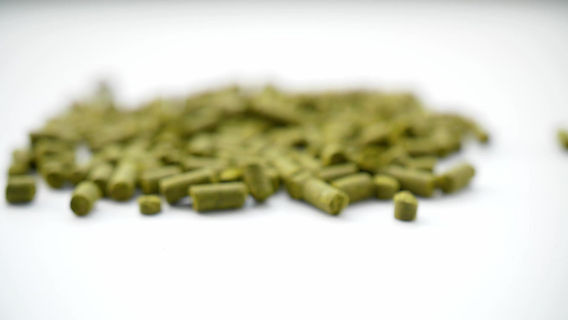
bottom of page